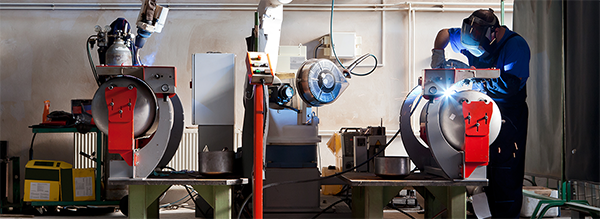
Control your tribal business risks with lockout/tagout safety
Designed to protect employees involved in service and maintenance activities, lockout/tagout safety measures guard against the unexpected start-up of machines or equipment or the release of stored energy that could cause injuries. More prevalent in manufacturing companies, a lockout/tagout safety program can also be used at a bakery, print shop, or hotel’s laundry and industrial kitchen – even a bowling alley.
The unexpected activation of machinery or process equipment during maintenance operations can have tragic consequences. That’s why it’s important your employees are aware of the various types of equipment and their energy sources, along with their hazards.
The good news is – it’s not an expensive proposition. Implementing an effective lockout/tagout program doesn’t require a heavy investment of time or money.
Creating your lockout/tagout safety program
An effective lockout/tagout program includes the following actions:
- Establishing an energy control program, including period inspections.
- Developing, documenting and utilizing lockout/tagout procedures.
- Providing employees with appropriate training.
- Providing equipment required to perform lockout/tagout procedures.
- Ensuring continued competency through inspections and retraining.
When creating your program, here are a few of the questions you’ll need to answer:
- Who should be authorized to lockout?
- Where are all relevant energy components, disconnecting points, blocking, discharging and bleeding points?
- Should associated and/or adjoining equipment be locked out?
- Are lockout procedures customized to the unique needs of each piece of equipment?
- When purchasing new machines, is priority given to those that workers can most easily control for hazardous energy?
At the very least, your program should include these steps:
- Shutting down the system or equipment.
- Verifying that all moving parts have stopped.
- Locking and tagging each energy-isolating device in the proper sequence and with appropriate lockout devices.
- Verifying that each lockout has accomplished its purpose and the equipment is completely isolated from all energy sources.
- Neutralizing all stored energy and verifying that the system has been neutralized.
Related: Confined Space Safety Tips For Tribal Employees
When to tagout, when to lockout?
Tags simply provide a warning; they don’t block employees or anyone else from access. Everyone understands the meaning of locks. When the employer decides whether lockout or tagout is the best method, employees must make sure the locks or tags are effective. The employer will provide equipment — chains, wedges, blocks, etc. to secure access.
Lockout devices hold energy-isolation devices in a safe or “off” position. As positive restraints, they provide protection by preventing machines or equipment from becoming energized, because no one can remove them without a key or other unlocking mechanism, or through extraordinary means, such as bolt cutters.
Tagout devices, by contrast, are prominent warning devices that an authorized employee fastens to energy-isolating devices to warn employees not to reenergize the machine while he or she services or maintains it. Tagout devices are easier to remove and, by themselves, provide employees with less protection than do lockout devices.
Whenever choosing tagout over lockout, you must provide employees the same level of safety that lockout procedures would: “full employee protection.” This means you as the employer should take the extra step to make sure that tagout is the best method.
Lockout is preferred over tagout for the following reasons:
- Locks are very difficult to remove; employees can easily remove tags.
- Locks are considered safety devices; tags generally serve as only a warning and are not considered a safety device.
- Chemicals or materials can also damage tags; they can also be easily lost.
Choose a lockout program (or tagout program that provides a level of protection equal to that achieved through lockout) whenever your employees engage in service or maintenance operations on machines that are capable of being locked out and that expose them to hazardous energy from unexpected energization, startup, or release of stored energy. Your device can be locked out if it meets one of these requirements:
- It’s designed with a hasp or other part to which you can attach a lock such as a lockable electric disconnect switch
- It has a locking mechanism built into it
- It can be locked without dismantling, rebuilding, or replacing the energy-isolating device or permanently altering its energy-control capability, such as a lockable valve cover or circuit breaker blockout.
The primary way to prevent the release of hazardous energy during service and maintenance activities is by using energy-isolating devices such as manually operated circuit breakers, disconnect switches, and line valves and safety blocks. Lockout requires use of a lock or other lockout device to hold the energy-isolating device in a safe position to prevent machinery from becoming reenergized. Lockout also requires employees to follow an established procedure to ensure that machinery will not be reenergized until the same employee who placed the lockout device on the energy-isolating device removes it.
Establishing daily procedures
Shift change: A critical lockout/tagout safety time
The shift change is one of the most potentially dangerous situations on a job site with lockout/ tagout possibilities. If a worker leaves a machine without removing his/her personal lock or tag, the worker coming on is left confused and may come in and do the wrong thing.
Here are three ways to prevent some of these possible safety problems:
Work permit. Lockout/tagout devices are not removed during shift or personnel changes. Instead, a work permit is re-issued after each shift or personnel change, allowing the oncoming authorized employee the opportunity to inspect the equipment.
Operation locks. This procedure determines that the master lock is the first lock applied to the equipment after it’s de-energized and the last to be removed. Each employee attaches his or her personal lockout/tagout device while working and removes it after the work has been completed.
Temporary tagout. Outgoing employees remove their lock or tag before the next employee arrives. At the time the personal lock is removed, the outgoing employees should apply a tag. This tag will have space for the outgoing employee to sign his or her name, date and time. The next employee could then verify that the equipment was deenergized before applying his or her personal lock and removing the temporary lock.
Related: 5 tools to prevent tribal workplace fall hazards
What must workers do before they begin service or maintenance activities?
Before beginning service or maintenance, the following steps must be accomplished in sequence and according to the specific provisions of the employer’s established procedures:
- Prepare for shutdown.
- Shut down the machine.
- Disconnect or isolate the machine from the energy source(s).
- Apply the lockout or tagout device(s) to the energy-isolating device(s).
- Release, restrain, or otherwise render safe all potential hazardous stored or residual energy. If a possibility exists for reaccumulation of hazardous energy, regularly verify during the service and maintenance that such energy has not reaccumulated to hazardous levels; and
- Verify the isolation and deenergization of the machine.
What must workers do before they remove their lockout or tagout device and reenergize the machine?
Employees who work on deenergized machinery may be seriously injured or killed if someone removes lockout/tagout devices and reenergizes machinery without their knowledge. Thus, it is extremely important that all employees respect lockout and tagout devices and that only the person(s) who applied these devices remove them.
Before removing lockout or tagout devices, the employees must take the following steps in accordance with the specific provisions of the employer’s energy-control procedure:
- Inspect machines or their components to assure that they are operationally intact and that nonessential items are removed from the area.
- Check to assure that everyone is positioned safely and away from machines.
After removing the lockout or tagout devices but before reenergizing the machine, the employer must assure that all employees who operate or work with the machine, as well as those in the area where service or maintenance is performed, know that the devices have been removed and that the machine is capable of being reenergized.
Lockout/tagout safety communication
Make messages site-specific, but don’t rely on words alone. Symbols also are appropriate, as long as they’re consistent and convey the same warning as the written message. You’ll want to tailor the message so that it’s appropriate to that particular device such as:
DO NOT START.
DO NOT OPERATE.
DO NOT OPEN.
DO NOT CLOSE.
DO NOT ENERGIZE.
Additionally, you’ll want to ensure that:
- Employees can easily recognize each lockout/tagout device. Clarity is crucial so that employees don’t mistake the device for anything else.
- You only use the device on the machine. If there’s more than one device on the machine, it may confuse employees.
- You don’t use the lock for any other purpose. The lock loses its importance if it’s been used for anything else.
- The lock is durable, holding up to the environment, chemicals, temperature extremes or any other problem it may endure.
- The lock must be identifiable by everyone who’ll have anything to do with it.
Related: Material Handling Improvements in Your Tribal Workplace
Who should we include in training on lockout/tagout safety?
Safety experts agree that three groups of employees should be trained:
Authorized employee. This is the employee who will physically perform the lockout/tagout and the servicing of the machine. Trained at least annually, this employee should be well-versed on all facets, including:
- Hazardous energy recognition
- Type and magnitude of energy present
- Types and quantities of energy control devices
- Isolation
- Points of control
- Lockout/tagout devices
- Lockout procedures
- Re-energizing procedures
Affected employee. This employee will operate the equipment that the authorized employee is servicing. This employee is trained initially and again if there’s a change in job assignment or a change in equipment. The affected employee must:
- Immediately recognize lockout/tagout devices
- Know the purpose of lockout/tagout devices
- Determine when a control procedure is in use
- Know not to disturb lockout/tagout devices
- Know the danger of violating procedures
Other employees. These employees receive training for different reasons. While they are taught the purpose of lockout/tagout safety, they also are taught to never touch any locks, tags or equipment covered under the program. This training is done during new employee orientation, through the use of employee handbooks and through regularly scheduled safety meetings.
By setting your lockout/tagout safety procedures in writing, implementing your policies, training your employees and periodic check-ups, you’ll have taken great steps to preventing workplace injuries.